Expert packaging machine repair service for industrial needs.
Expert packaging machine repair service for industrial needs.
Blog Article
Why Timely Packaging Equipment Repair Service Provider Are Essential for Functional Performance
In the competitive landscape of production, the duty of prompt product packaging maker repair solutions can not be overemphasized. Such solutions are vital not only for minimizing unplanned downtime but likewise for cultivating a smooth manufacturing environment that satisfies consumer needs. By attending to minor malfunctions prior to they rise, companies can significantly boost functional efficiency and lower lasting costs. Nonetheless, the effects of overlooking these solutions expand beyond prompt repair work, questioning regarding devices integrity and overall efficiency. What strategies can companies apply to guarantee they stay aggressive in their upkeep strategy?
Effect of Downtime on Production
Downtime in manufacturing can be compared to a ship adrift mixed-up; without a trustworthy training course, production processes can promptly drift off track. The effect of downtime, particularly in packaging operations, can be both instant and far-ranging. When equipment breakdowns, manufacturing halts, resulting in a backlog of orders that can strain client connections and credibility. Each min lost translates right into revenue loss, as business have a hard time to fulfill market need and fulfill dedications.
Furthermore, unintended downtime disrupts process, resulting in inadequacies that resound throughout the supply chain. Employees may be left idle, resulting in reduced morale and performance. In addition, the price of emergency situation repair services typically exceeds that of set up maintenance, additional stressing monetary resources.
In a competitive landscape, where time-to-market is essential, the ability to keep consistent production levels comes to be paramount. Downtime not only impacts instant result yet can also develop a causal sequence that affects stock degrees, money flow, and general functional efficiency - packaging machine repair service. Thus, understanding and minimizing the influence of downtime is crucial for suppliers intending to maintain their one-upmanship and make certain lasting growth
Benefits of Regular Maintenance
Routine maintenance of product packaging devices functions as a vital column in ensuring nonstop manufacturing and functional efficiency. By carrying out a consistent maintenance timetable, services can significantly improve the integrity and longevity of their devices. Routine evaluations enable the prompt recognition of damage, stopping small issues from intensifying into major breakdowns.
Additionally, normal maintenance maximizes device performance, guaranteeing that product packaging procedures run at peak efficiency. This optimization not just enhances throughput but additionally lessens the chance of item issues, therefore keeping top notch standards. Well-maintained equipments contribute to energy performance, decreasing functional prices linked with too much power consumption.
Along with performance benefits, normal maintenance promotes a safer working setting. By making sure that devices operate properly, the threat of accidents and injuries triggered by equipment failing is notably reduced. This dedication to safety not only secures staff members yet also straightens with governing conformity, alleviating potential legal obligations.
Eventually, buying regular maintenance enhances total productivity, decreases unforeseen downtime, and promotes a culture of aggressive property administration. This tactical strategy guarantees that product packaging procedures remain affordable in a busy market, which is essential for sustained success.
Price Ramifications of Postponed Repair Services
Ignoring prompt repairs on product packaging equipments can bring about considerable monetary consequences for services. When equipment breakdowns, production lines can halt, causing lost result and postponed distribution routines. packaging machine repair service. Each hour of downtime translates right into find not only lost sales but likewise prospective penalties from customers because of unmet due dates
Furthermore, delayed repairs can worsen existing issues, leading to much more severe damages and enhanced fixing expenses in time. A minor breakdown could escalate into a major breakdown, necessitating pricey parts substitute or a complete overhaul of the maker. This can stress budgets and divert funds from other critical areas, impeding overall operational growth.
Furthermore, organizations may deal with raised labor expenses as workers stay still or are reassigned throughout expanded repair work periods. The longer machinery is out of service, the more significant the influence on workforce efficiency.
Enhancing Equipment Longevity
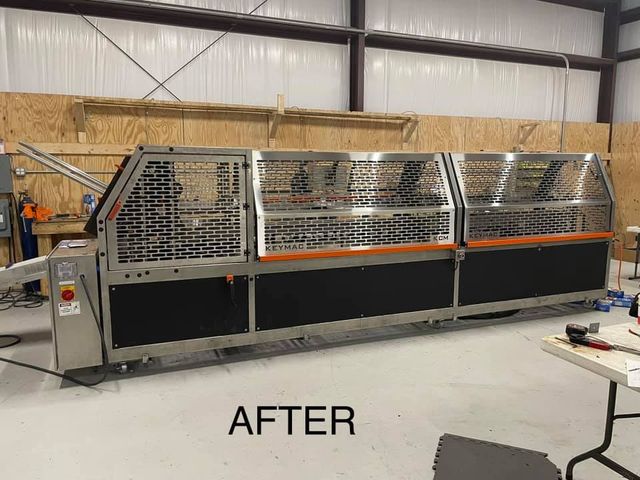
Implementing a regular upkeep timetable can recognize wear and tear early, stopping little issues from rising right into expensive malfunctions. This proactive strategy not just improves the device's operational reliability but likewise enhances the general production workflow. Operators must additionally guarantee that devices are used according to supplier requirements to prevent excessive stress on vital parts.
In addition, buying quality replacement parts during repair work contributes to tools durability (packaging machine repair service). Using subpar components may lead to regular failures, negating any kind of cost financial savings understood from less expensive fixings. Correct training for operators on ideal techniques for maker handling and operation can also substantially impact the devices's lifespan
Picking the Right Fixing Solution
Picking the proper repair service for product packaging makers is essential for ensuring very little downtime and optimum performance. When reviewing possible company, consider their market experience and specialization in packaging machinery. A business with a proven track document in dealing with similar tools will likely possess the needed knowledge to identify and settle problems efficiently.
Additionally, examine the availability of professionals and their feedback time to solution calls. A repair solution that provides 24/7 assistance can significantly minimize the impact of unexpected device failings. Inquire concerning their maintenance programs, as proactive service can stop pricey malfunctions and prolong the life-span of your devices.
Assess client reviews and testimonies to gauge the reliability and high quality of the solution. A reputable repair work service should have a background of his response completely satisfied clients that can confirm to their professionalism and performance. Lastly, take into consideration the expenses included, consisting of parts and labor. While cost is very important, focus on value-- ensuring that the solution fulfills your operational requirements without jeopardizing quality. By meticulously choosing the best fixing service, organizations can boost their functional effectiveness and reduce disruptions in manufacturing.

Final Thought
Finally, prompt product packaging equipment fixing services play a vital role in maintaining functional efficiency. By reducing unintended downtime, these solutions not just improve production flow but additionally add to cost financial savings and improved tools durability. Routine maintenance and punctual repair work serve to alleviate minor concerns before they intensify, consequently navigate to this site guaranteeing optimal machine efficiency. Inevitably, prioritizing prompt repairs promotes a trusted supply chain, bolsters staff member morale, and raises customer fulfillment through consistent item shipment.
Report this page